Safety Rigging
Matt Moltane • November 2, 2017
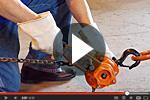
Check out this rigging safety resource, which is a fantastic way to further your team’s safety education:
Rigging Safety Webinars from Columbus McKinnon Corporation (USA-made rigging equipment supplier):
You’ll find immediate access to these three safety webinars:
- Rigging Part 1: Chain Sling Inspection
- Rigging Part 2: Proper Use of Shackles
- Rigging Part 3: Rigging with Lever Tools
You may also want to sign up to receive Alerts for their monthly safety webinars.
Dear Readers, This is the start of a new series of blog posts for our website. In this series, we will discuss safety programing, best practices in order to help organizations of all sizes prevent accidents and injuries in their workplaces, and help risk consultants help their clients in a better manner. The advice that will follow comes from our experience in the safety and risk control consulting fields. Look for more to follow!
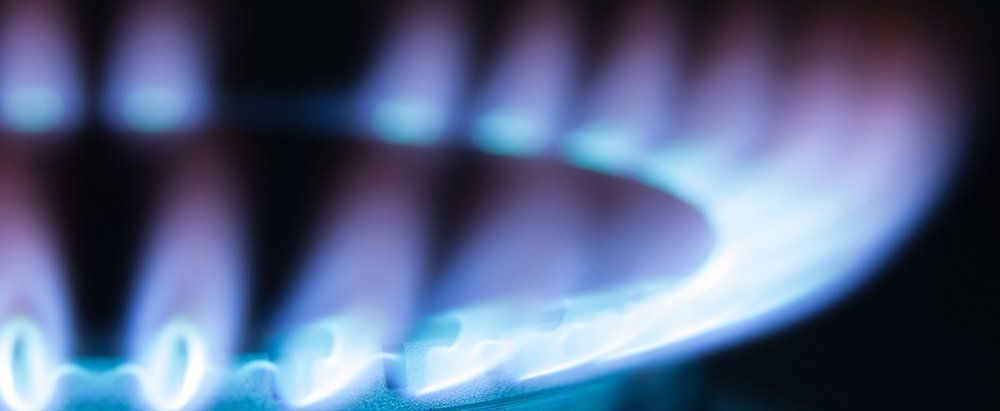
Natural gas is one of the safest energy sources available to homeowners and businesses alike. By itself, natural gas will not ignite. For ignition to occur, a mixture of gas between four and 14 percent must combine with air. Also, gas must have an ignition source with a temperature of 1,100 degrees Fahrenheit or more before it will ignite.